Know the specs of your fleet. Keep a detailed record of each truck’s length, width, height, and bed height. Remember, weight and air suspension systems can affect dimensions. So, make preliminary designs using Table 1, but for final decisions, use the actual measurements.
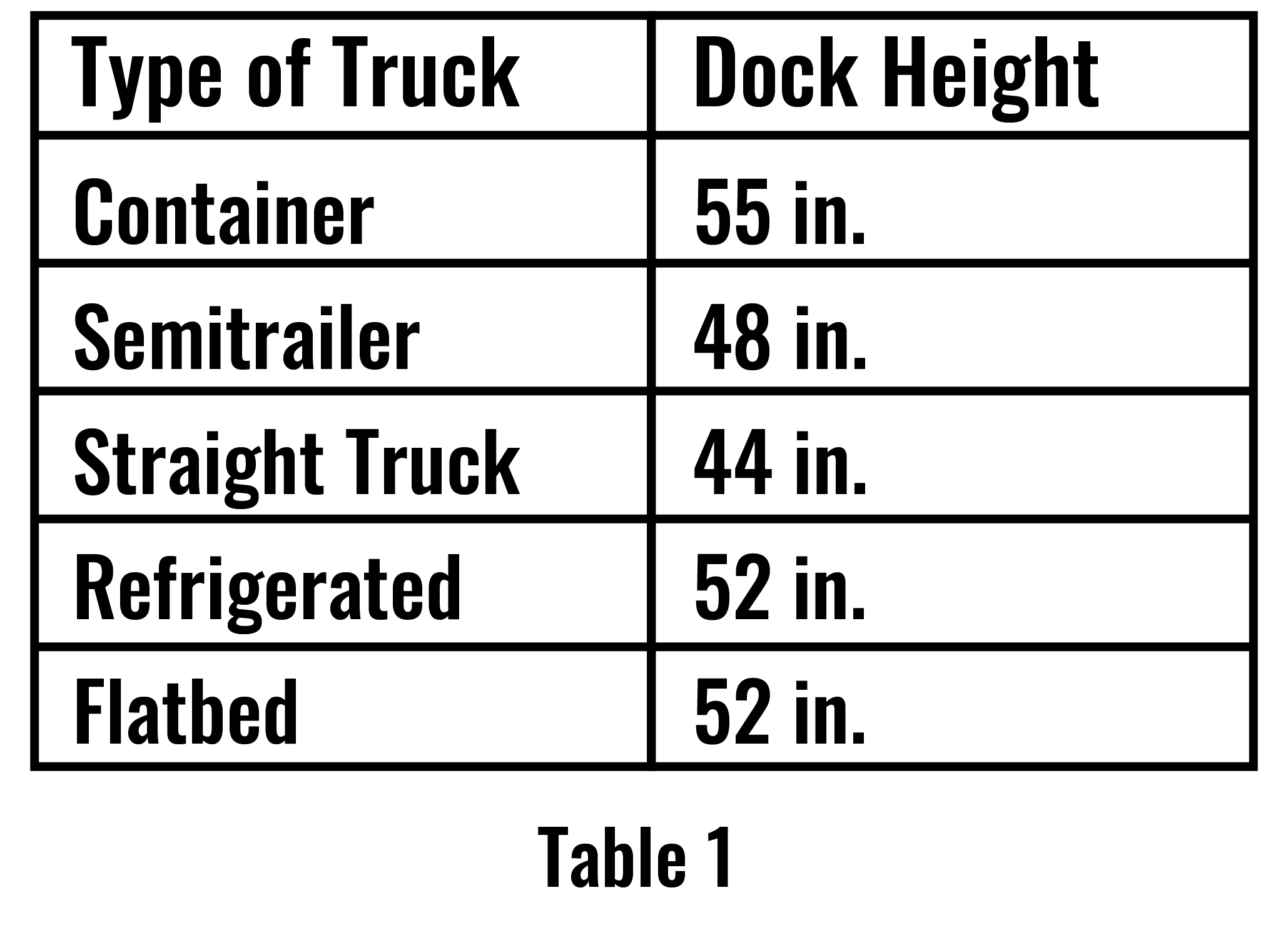
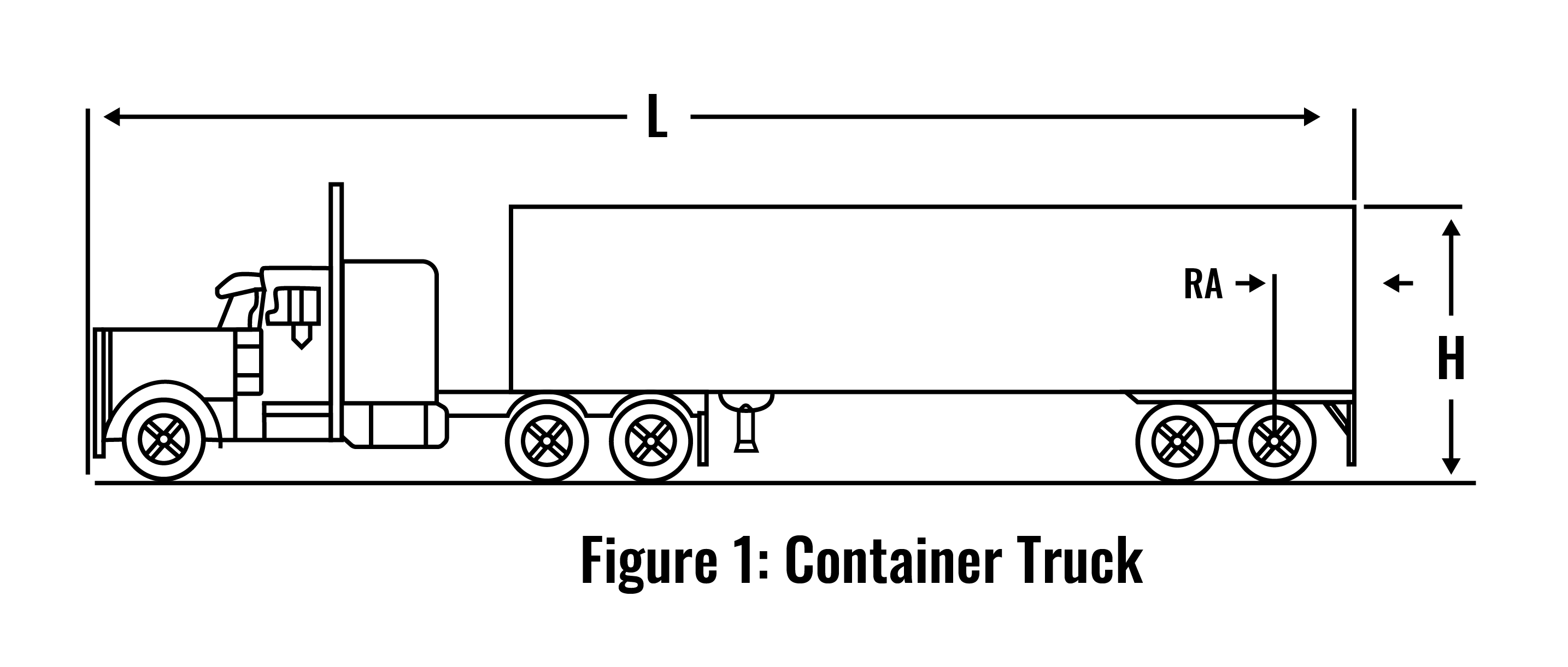
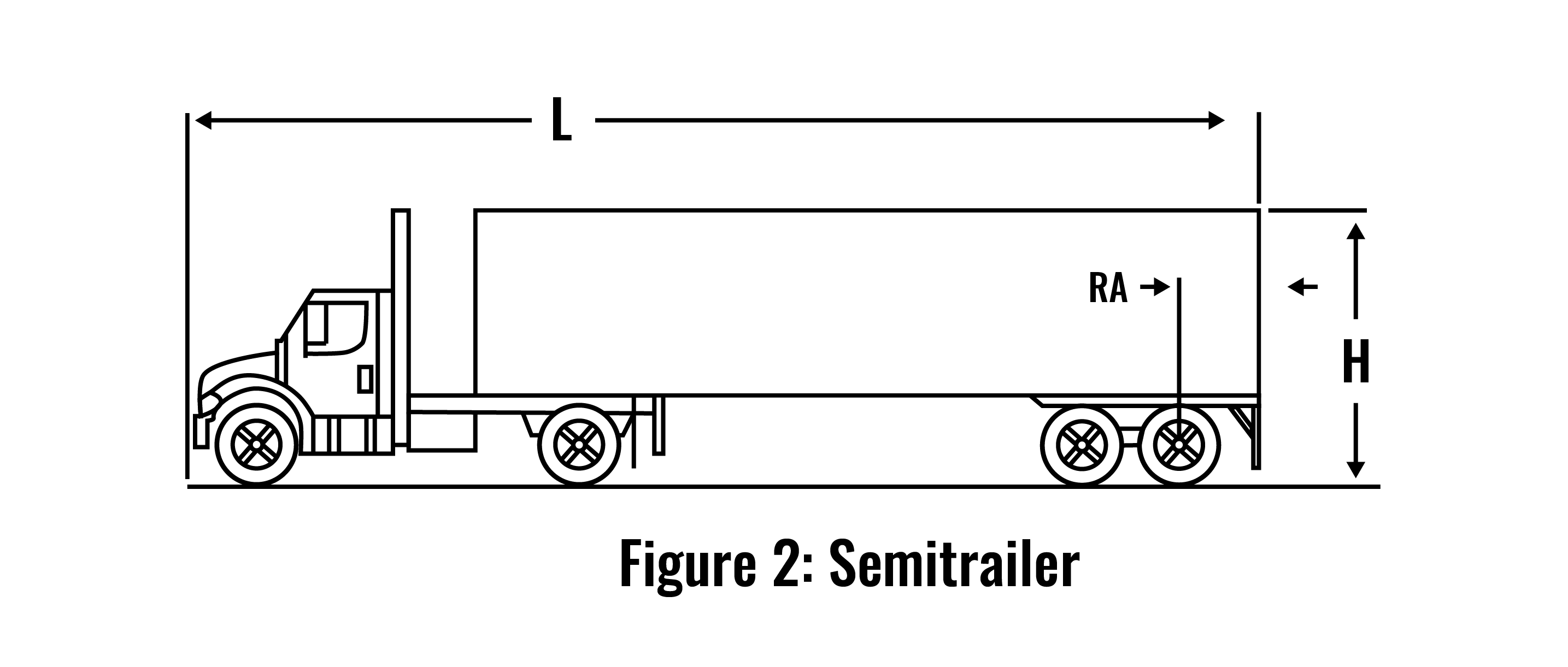
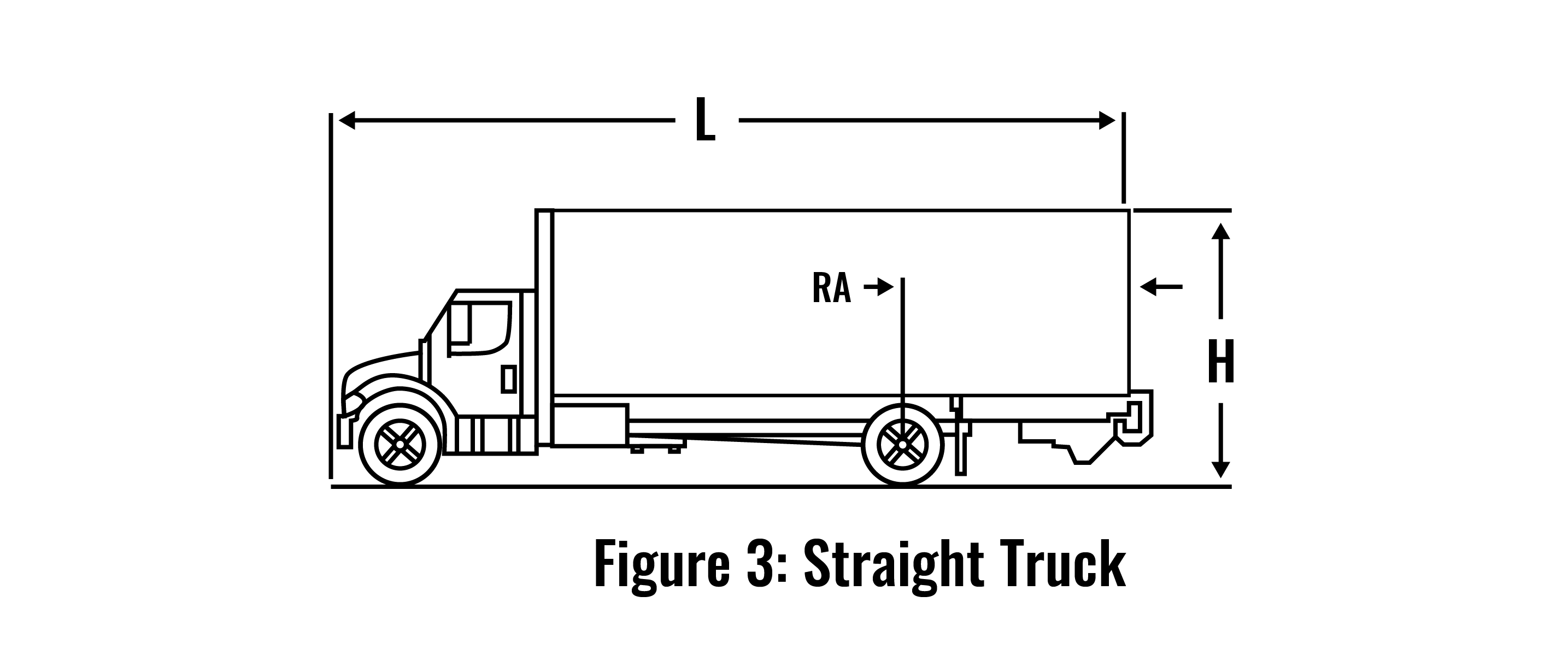
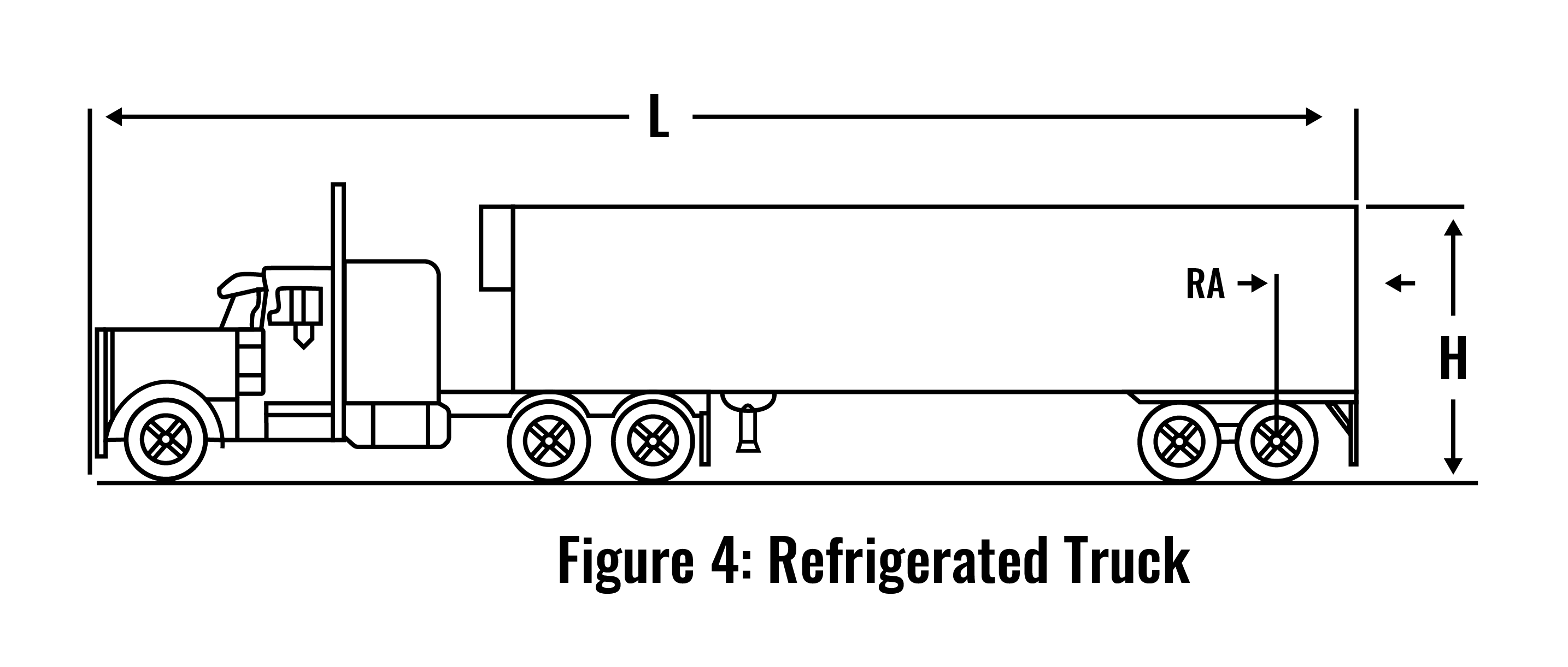
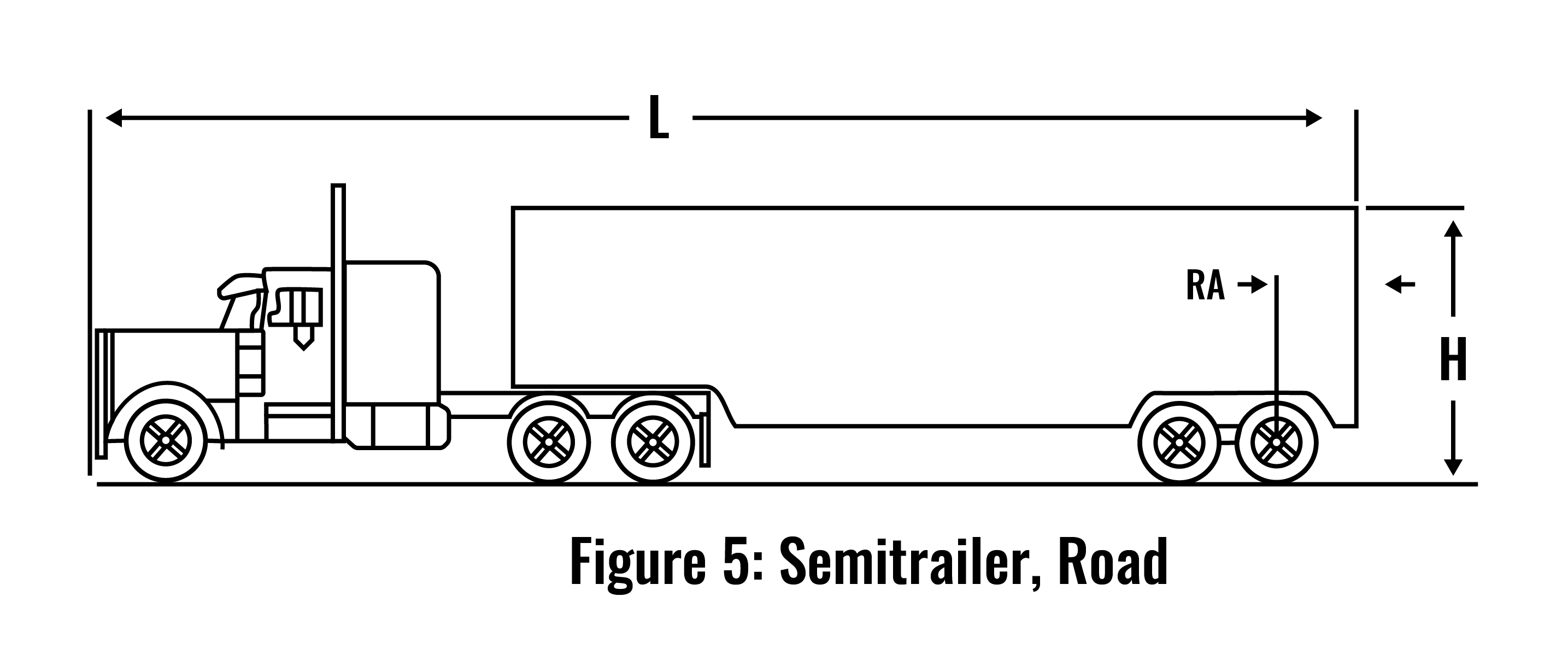
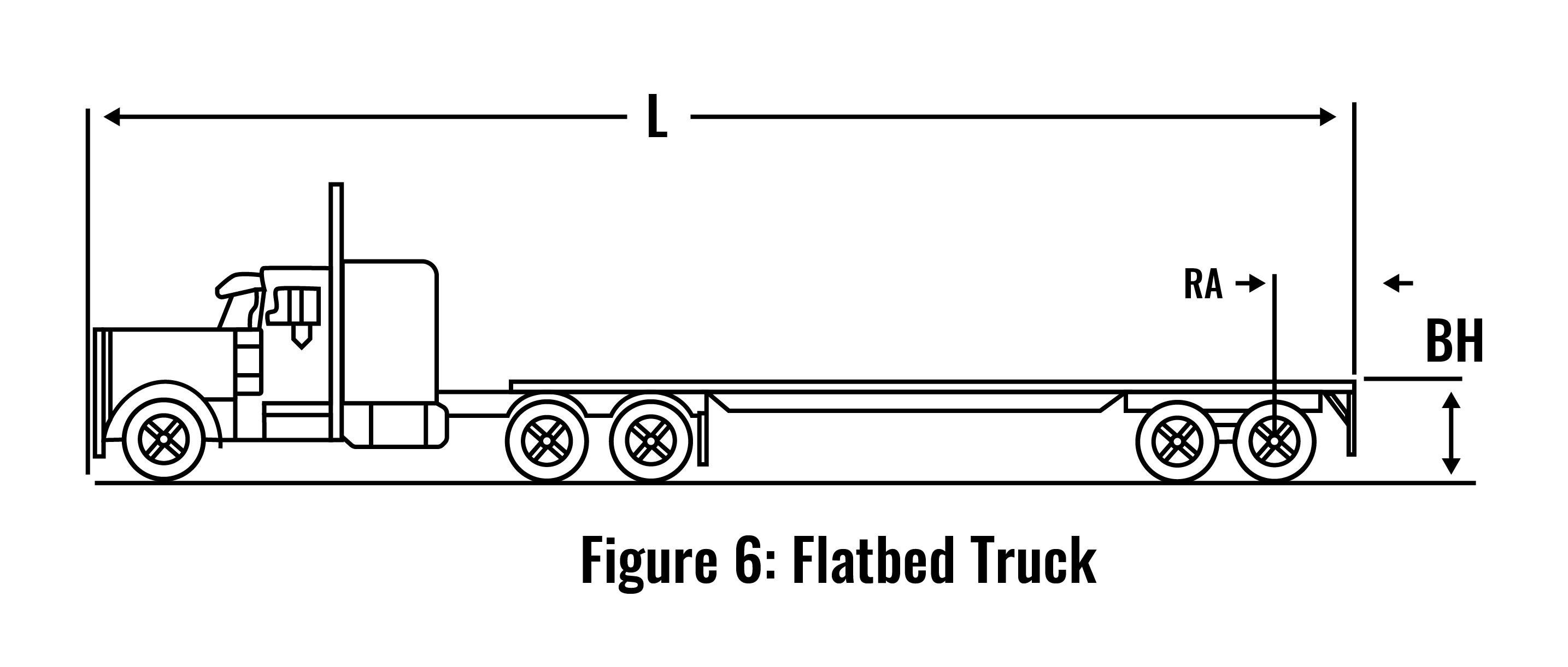
Sea and refrigerated containers can range from 30-62 inches. Accommodating this, along with lower-bed trucks, requires careful planning. Whether it’s various dock heights, hydraulic levelers, or elevating docks, find a solution that works for you. Remember to check out Table 2 for standard container sizes.
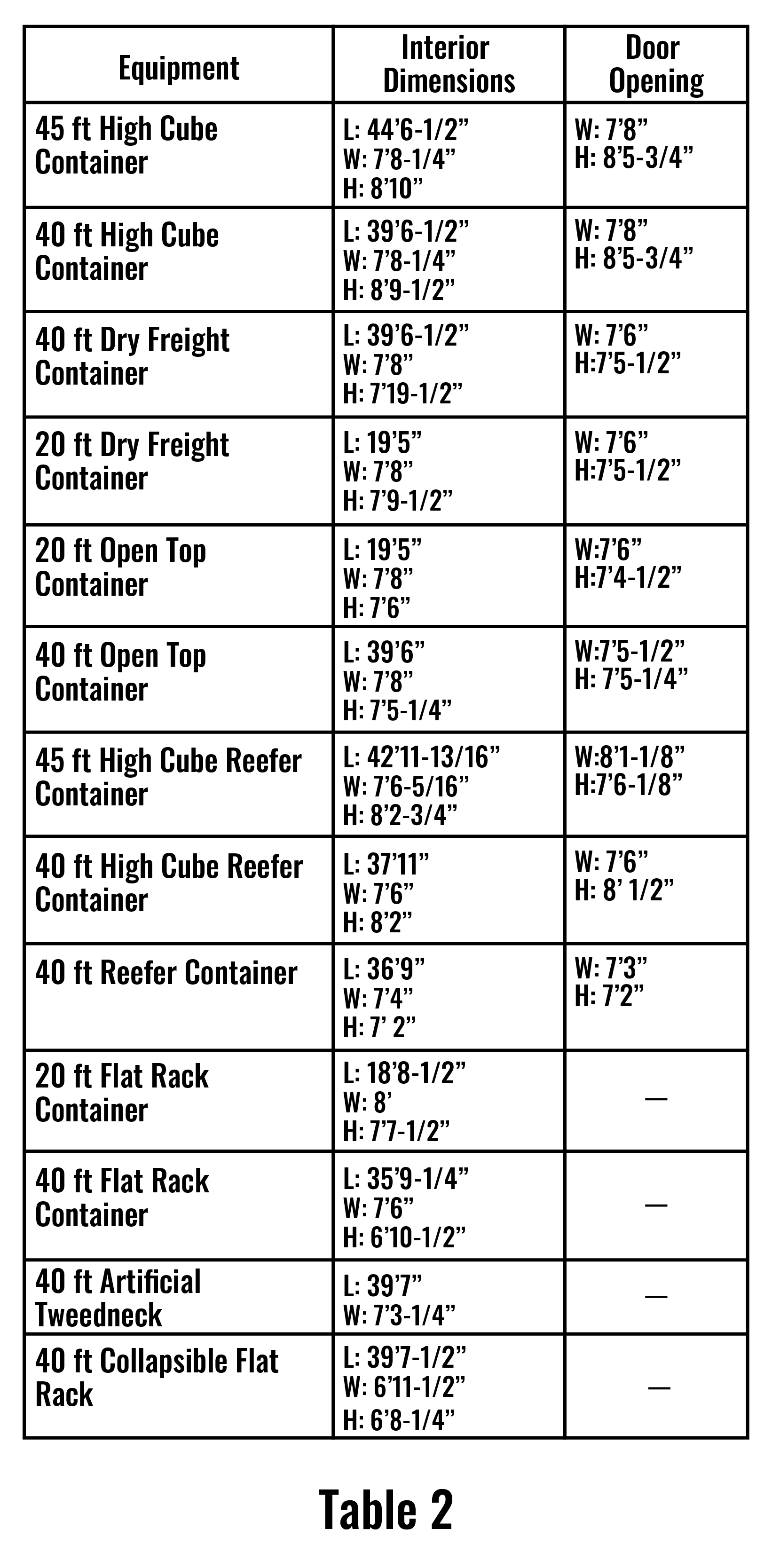
Also known as the Rear Impact Guard (RIG) bar, this is located at the trailer’s rear (Figure 7). This is where your restraint devices connect, ensuring safety during loading and unloading.
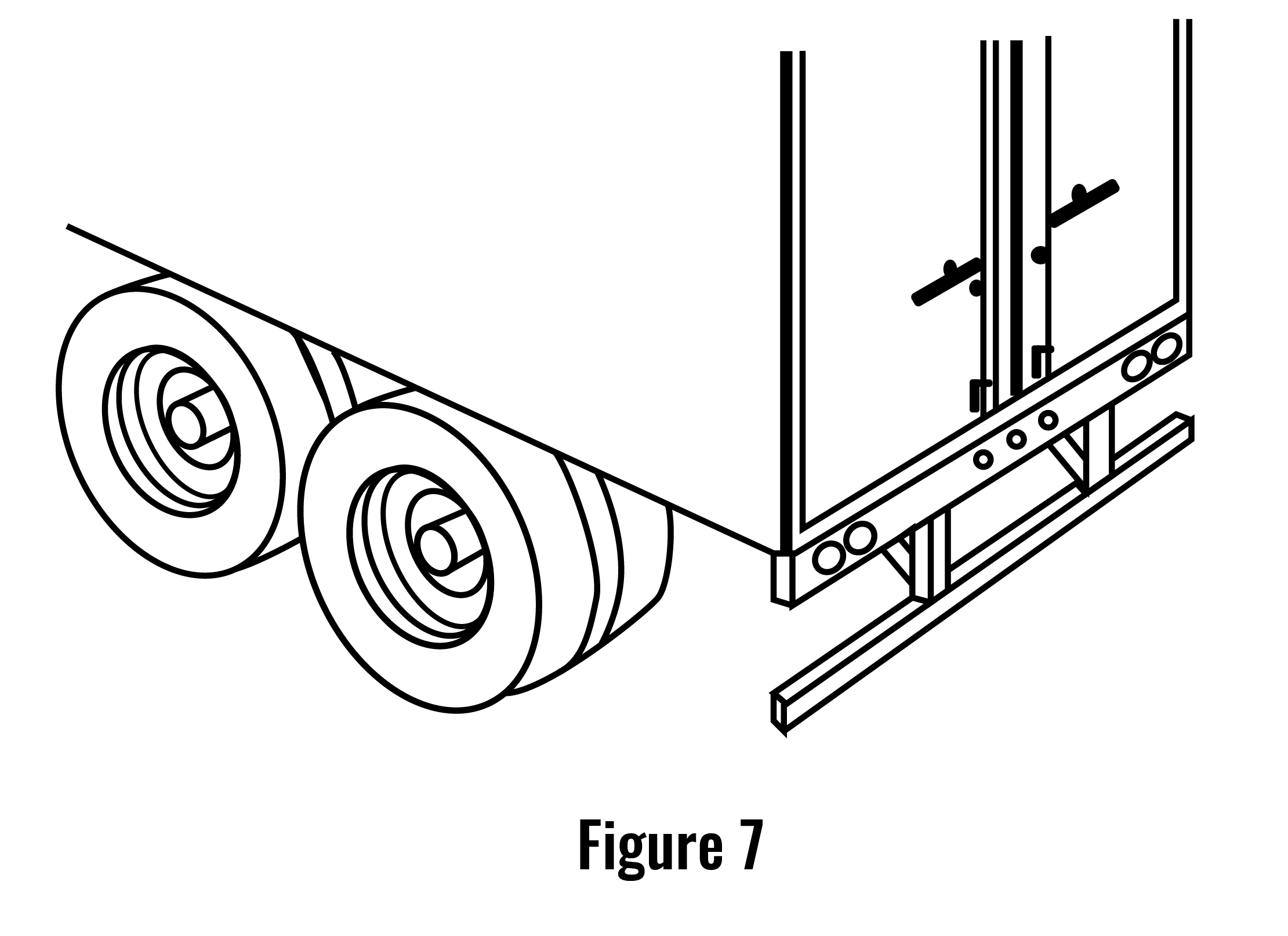
Dock height is central to your design and it needs to align with the height of your docking trucks. But remember, truck beds can rise and lower during loading and unloading. So, finding the midpoint of the bed heights of your expected trucks is key. See Table 3 for suitable dock heights for various types of trucks.
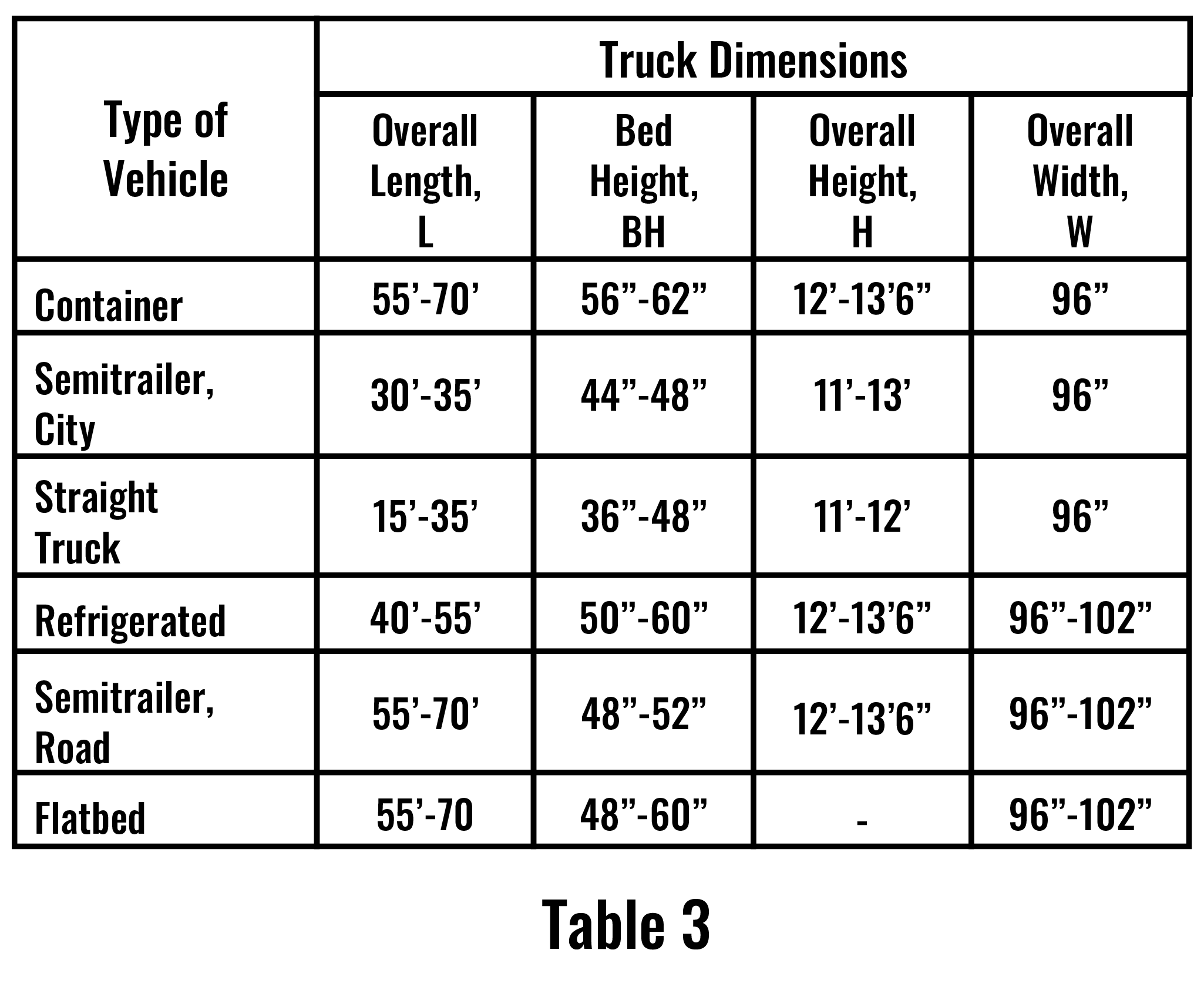
NOTE: Truck beds will rise and lower during loading and unloading
If the driveway is recessed, the dock height should be lower (Figure 8). A recessed parking area may lower the truck bed height by 6 to 10 in. For example, in Figure 9, the drive approach is an 8% decline leading to a level concrete pad at the dock. A typical trailer bed, which is at a 48 in. height (HL or height when level) from the decline drive, will be at approximately 40 in. (HD or height at dock) at the dock. Therefore, if the dock is intended to service trailers with 48 in. bed height, the dock height should be at 40 in.
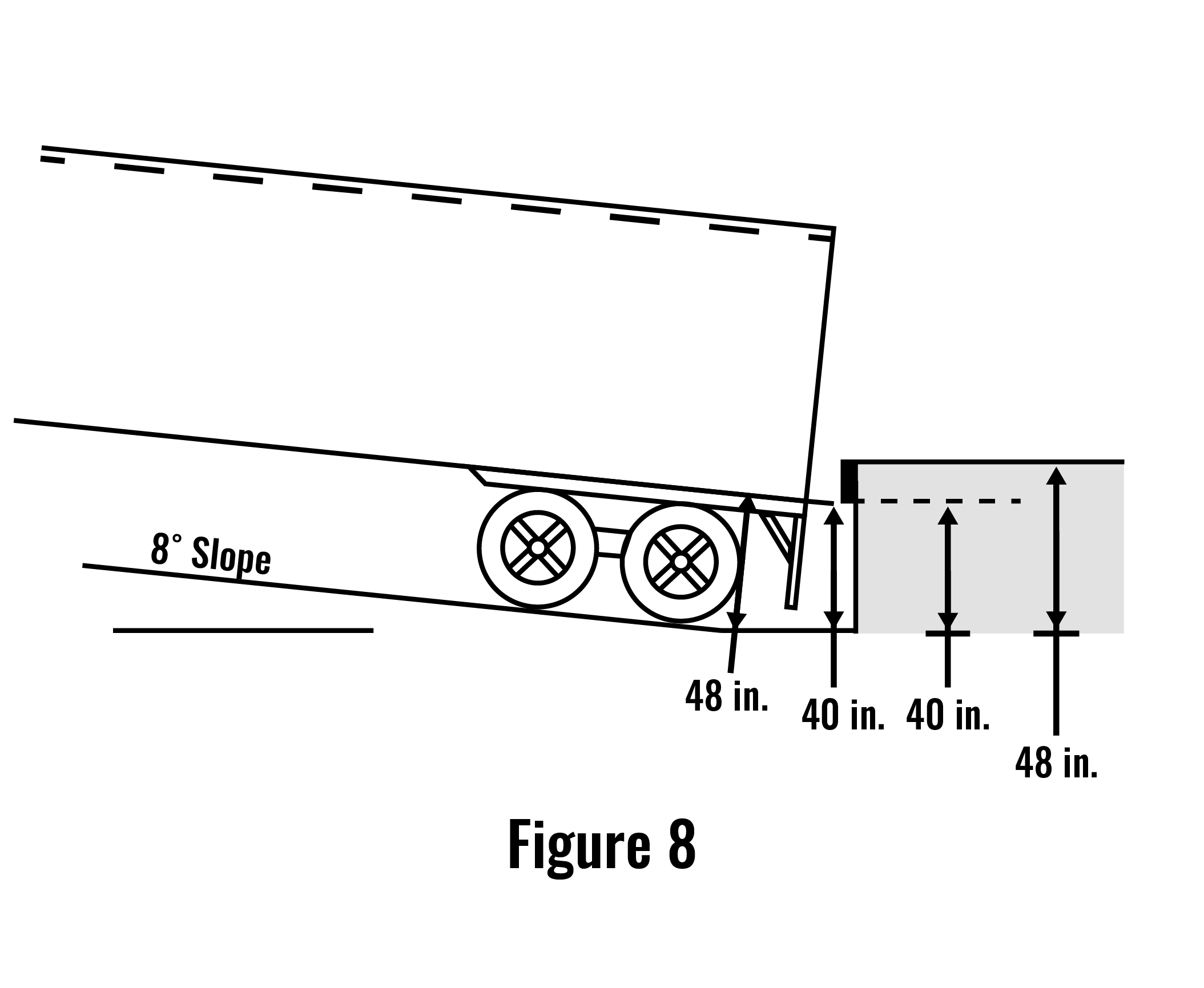

Design the dock height based on the specific parameters of driveway slope, geometry of the recessed parking area, and bed heights of the expected trucks unique to your building. If the expected trucks have very high or low bed heights, provide dedicated dock positions with special driveways and equipment, such as an elevating dock (Figure 10).
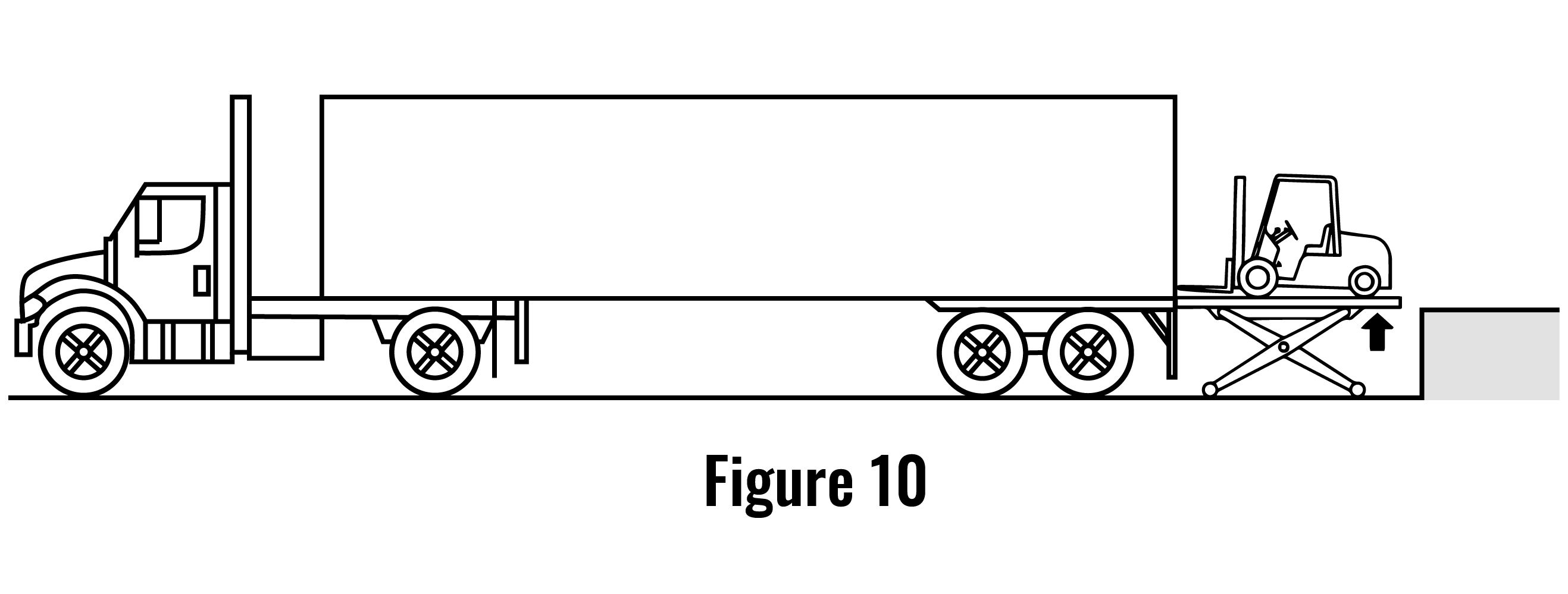
For open docks, where the trailer doors are commonly opened after the trailer is parked, design a dock height low enough for the door clamp hooks to clear the dock as they are opened (Figure 11). 51 in. is a common dock height for this situation. If the driveway is recessed, lower the dock height further since the doors swing down slightly as they are opened. Lower the dock by about 1 in. for each 1% of recessed driveway grade.
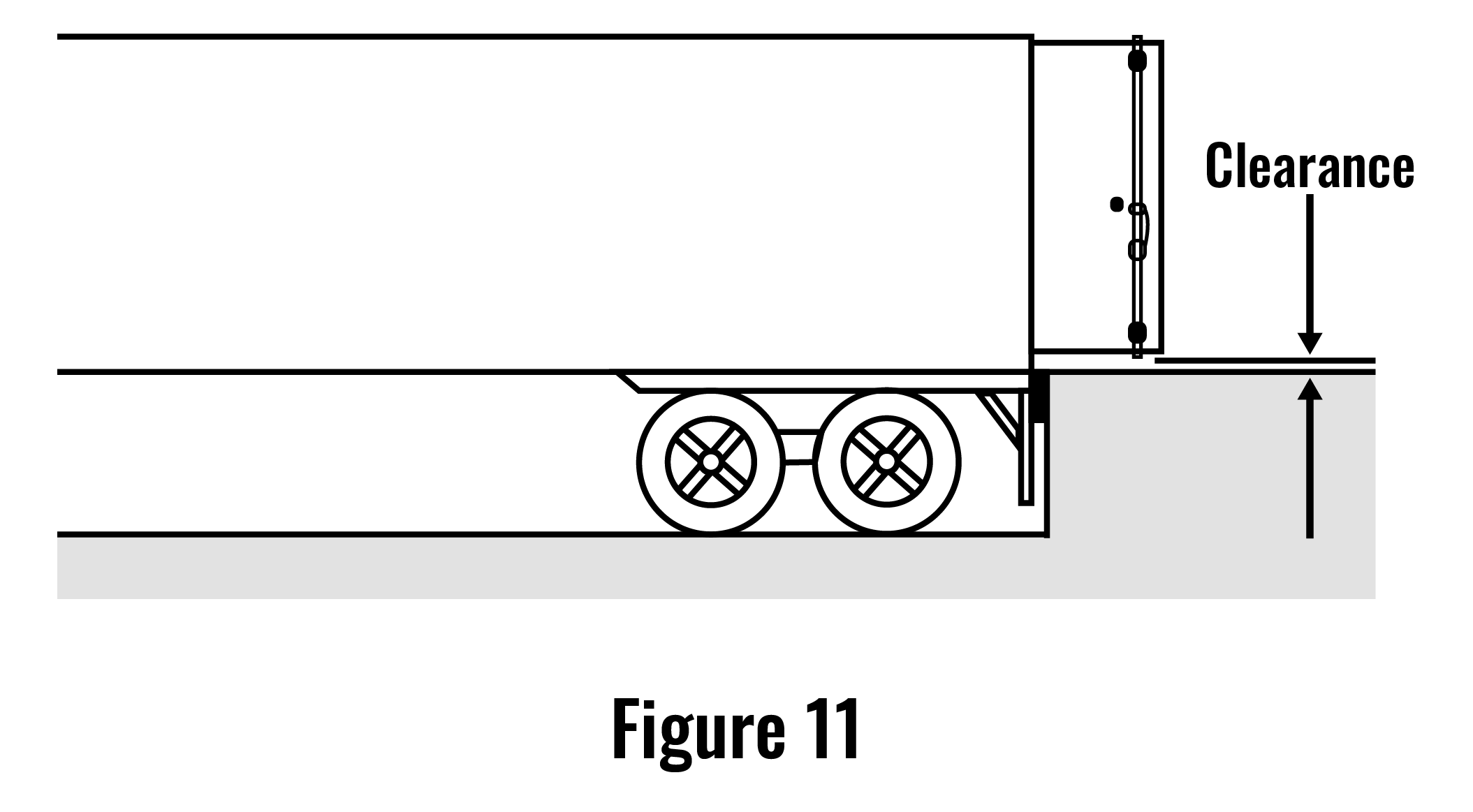
Each bay should be at least 12 feet wide to comfortably fit trailers, which are usually 8’0” to 8’6” wide, but a 14 ft wide design will reduce congestion (Figure 12). If swinging trailer doors will be opening or closing at the dock, the center distance should be at least 14 feet wide (Figure 12).
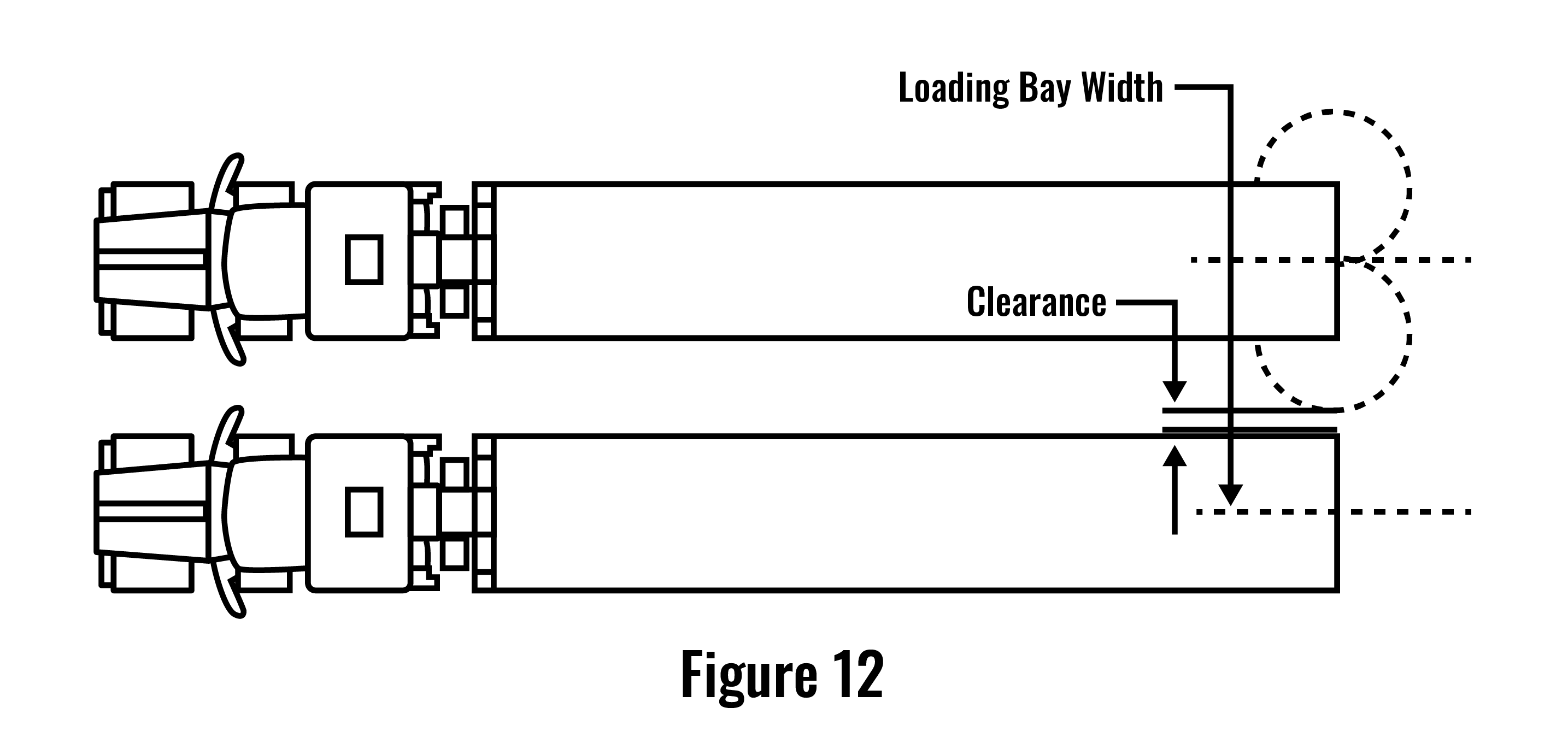
A vital component of inside/outside loading docks. Manual, overhead sectional doors or roller doors are common, with sectional doors offering a smoother, quieter operation. Sectional Doors are also insulated and thicker, adding extra strength.
NOTE: Always install door track protectors to protect the door tracks.
Common dock door dimensions are 8’0″ in width with 8 ft, 9 ft or 10 ft heights. Consider extending the door 13 ft to 14 ft above the driveway and a minimum of 8’6″ wide if full access to the truck’s interior is required.
The type of trucks being serviced, the sealing system, and environmental considerations should determine the door dimensions.
NOTE: The maximum trailer size limits are 8’6″ wide x 13’6″ high, varying by state. With a special permit, a flatbed may exceed the maximum width.
Width:
Dock doors narrower than 8’0″ are commonly installed with compressed foam dock seals for temperature control of refrigerated operations.
9 ft wide doors should be used to service 8’6″ wide trailers. Side-by-side palletizing is simplified, potential for product damage is reduced, and oversized loads can be serviced.
The doors should be between 8’6″ and 8’0″ wide to allow for trucks to park off-center. A 10 ft wide door can be designed for oversized loads. Note that wider doors require more building space, which may not be available.
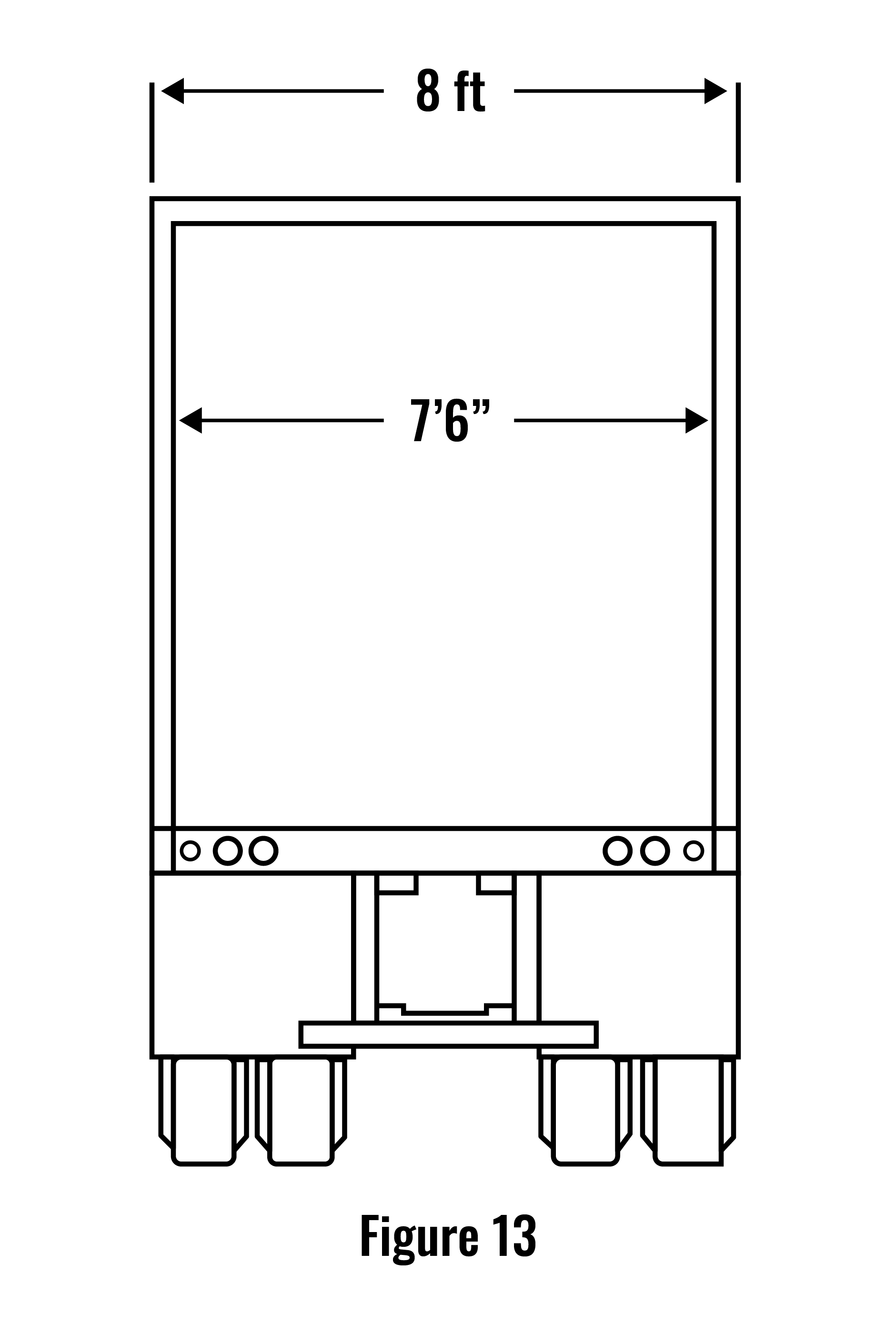
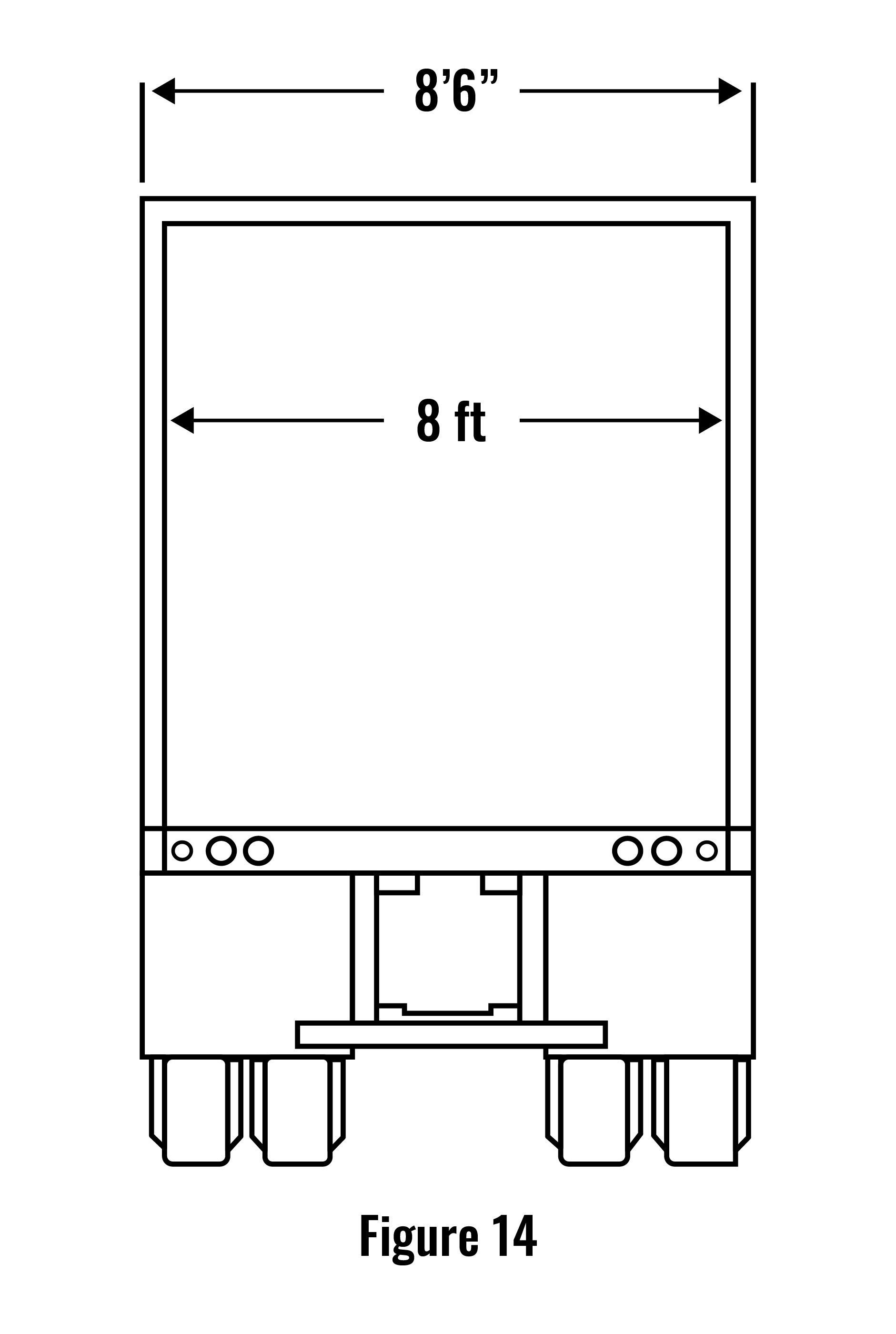
NOTE: Compression of seals may reduce the effective width and full access to trailer.
Heights:
Doors are typically 8 ft, 9 ft, or 10 ft high. 8 ft high doors can accommodate many loading and unloading operations where height is not critical, but cannot accommodate floor-to-ceiling loading (Figure 15). 8 ft high doors do not maximize the usage of the available height in the trailer, which leads to higher freight costs.
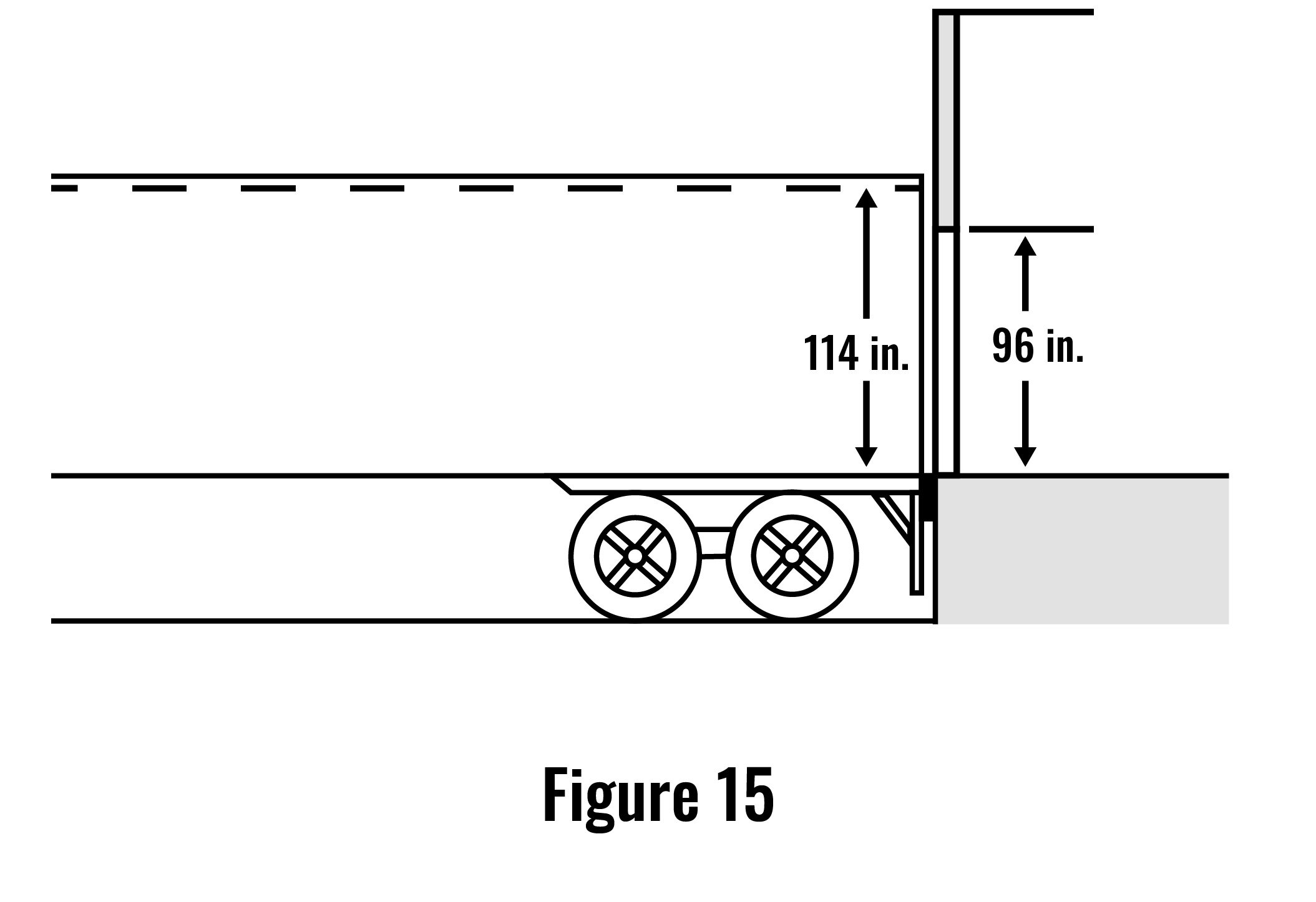
A 9 ft high door allows for improved floor-to-ceiling loading (Figure 16) as a higher load can pass through the door. Fuller, tighter loading makes for better space utilization with a decreased risk of product damage due to door impact. The 9 ft height suits a wide range of applications. However, in trailers with lower height, there may be a gap between the trailer and the top of the door. The gap can be closed off with a dock seal or shelter.
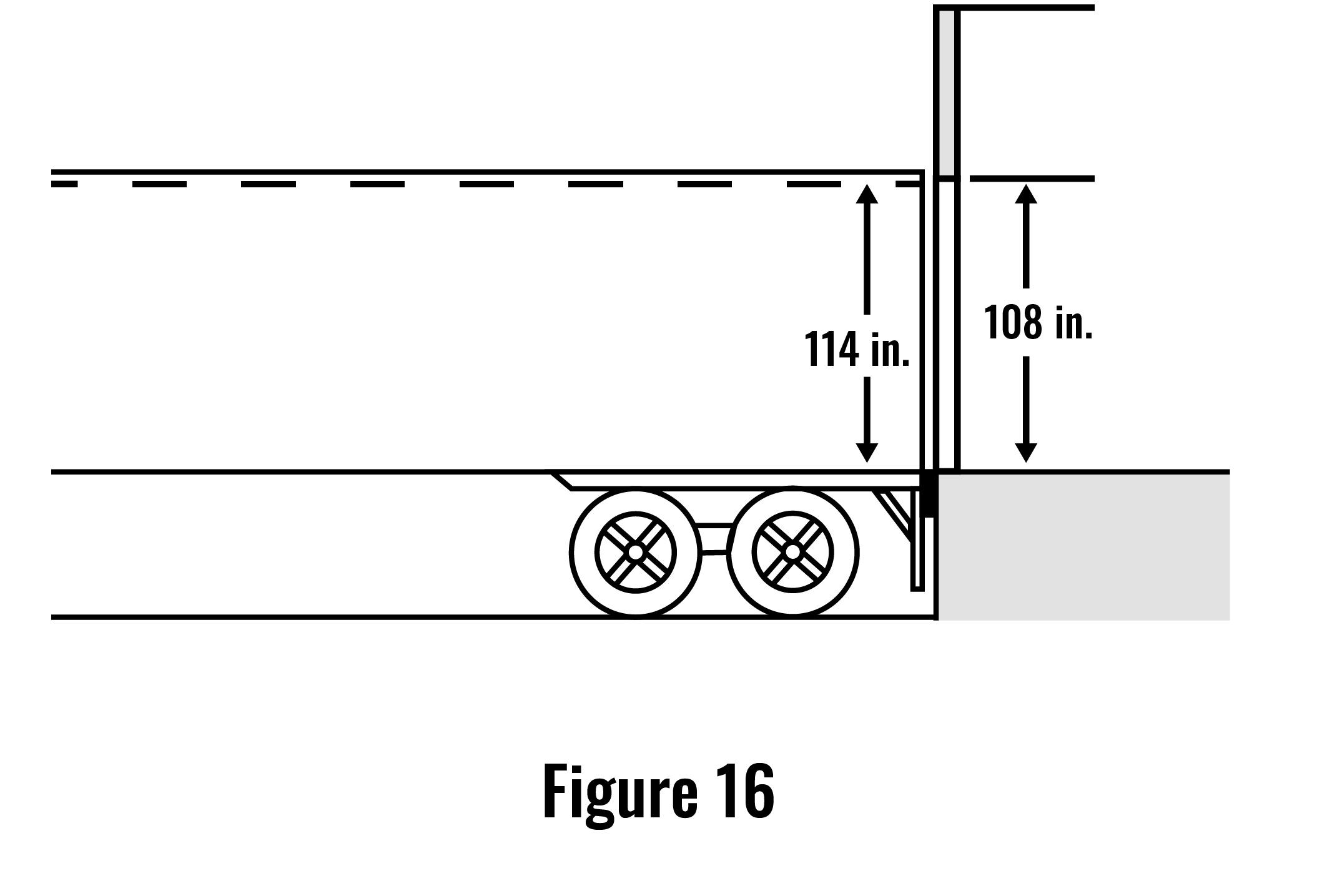
A 10 ft high door services the full range of loading and unloading operations (Figure 17). 10 ft high doors accommodate trailers of heights up to and including high cube trailers and high cube sea containers.
To provide full access to the entire width and height of a full-size trailer, the dock door should extend the full height of the trailer (13 to 14 ft) above the parking area.
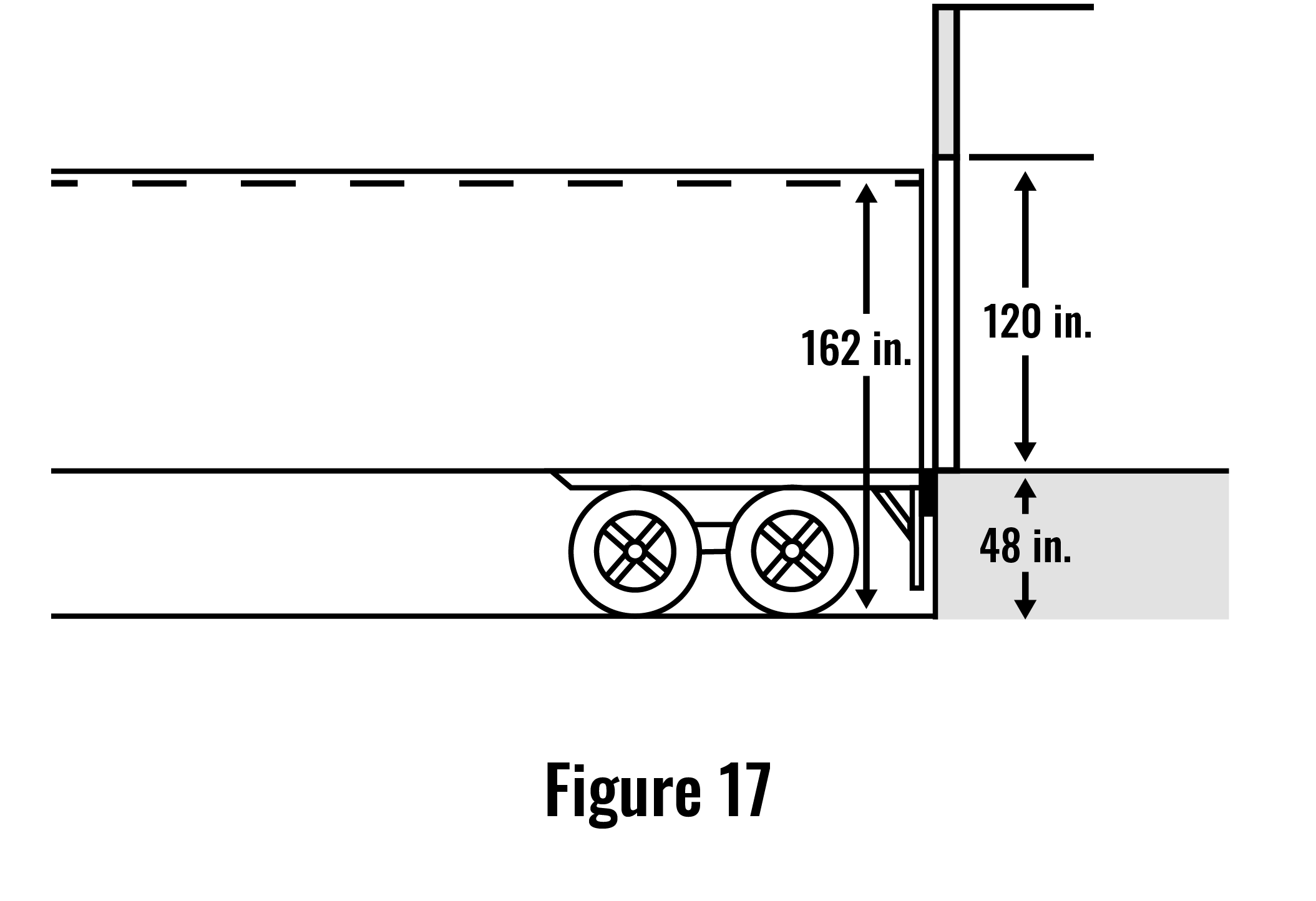
Design a forklift traffic aisle, 15 ft wide minimum, behind the loading ramps. This aisle provides better visibility, allows forklifts to maneuver behind the trailers, and permits two-way traffic parallel to the dock face. Aisles that are 15 ft or wider allow forklift drivers to drive straight onto the dock levelers, which reduces injury hazards and equipment stress (Figure 18).
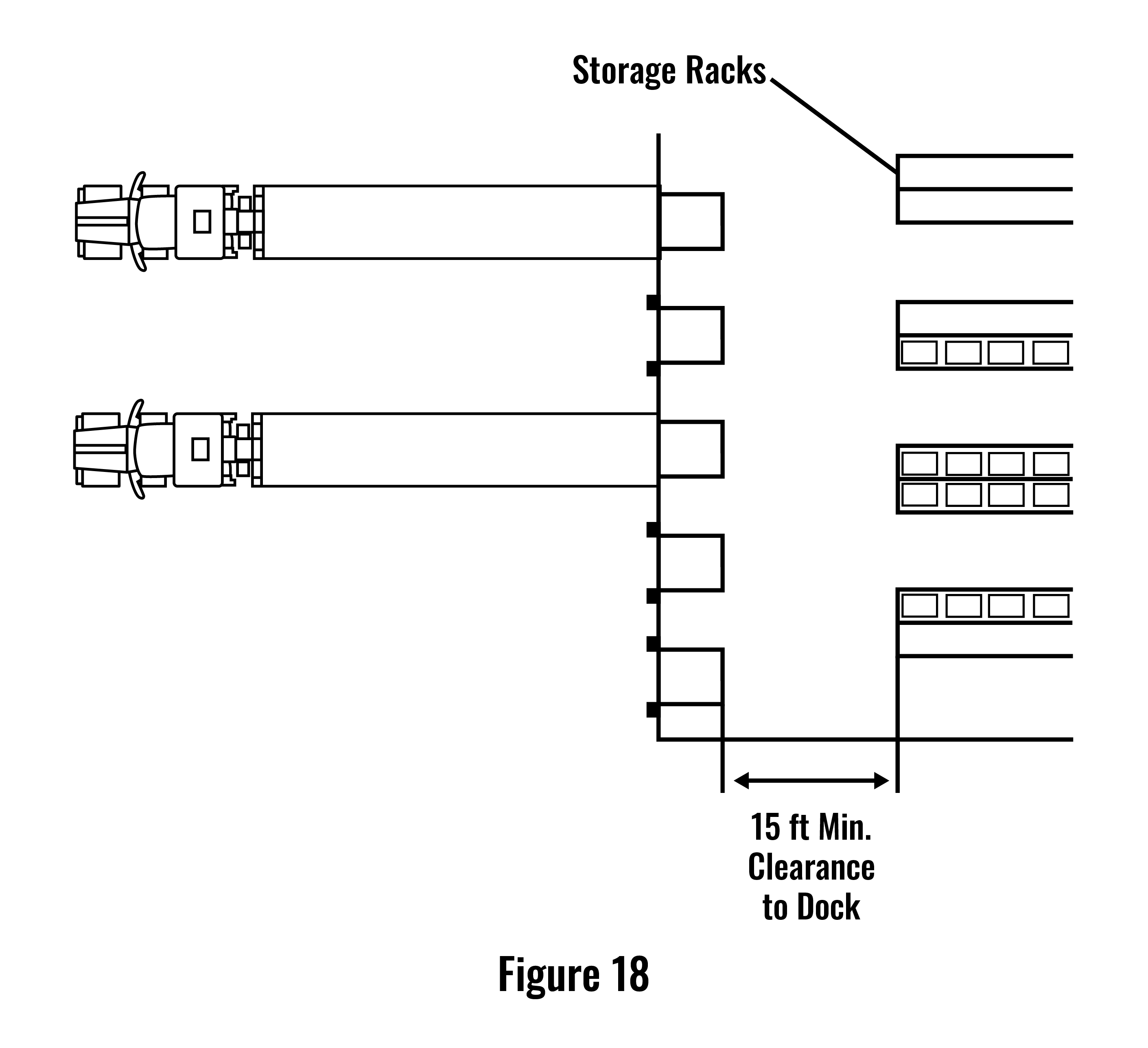
Implement restrictions to prevent forklift drivers from driving parallel to the dock face (Figure 19). This can prevent potential accidents with forklifts backing out of trailers.
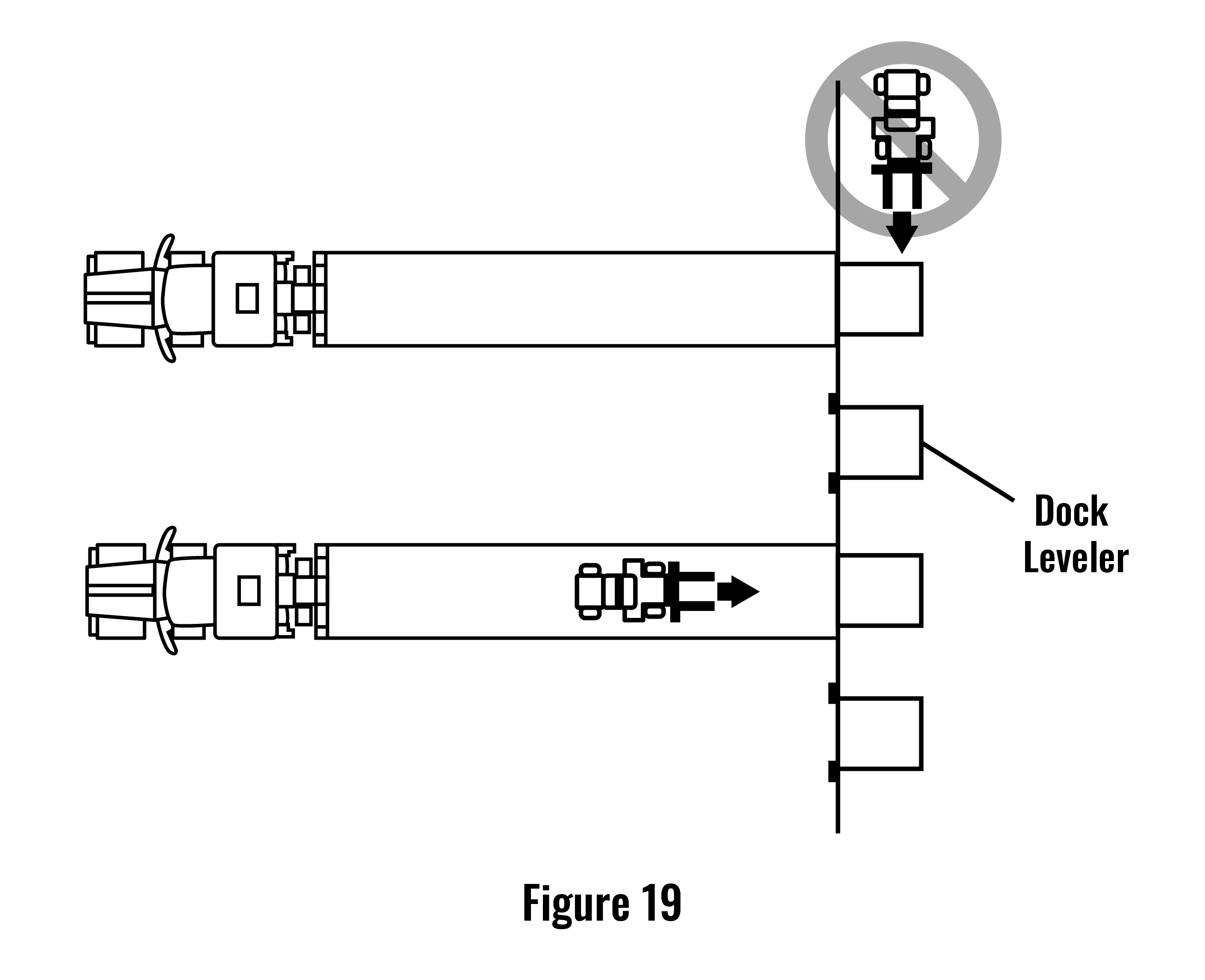
This guide should serve as a primer for designing your loading dock. By taking into account your unique specifications and the details listed above, you’ll be on the path to creating an efficient and safe loading dock for your operation.