Keeping a warehouse or distribution center running like a well-oiled machine is an arduous task. Every cog in the wheel needs to be in sync for the entire operation to function efficiently. What happens when a cog slips, causing unplanned equipment downtime? Chains are only as strong as their weakest link.
Many organizations find themselves unprepared when their supply chain operations grind to a halt due to equipment failure. This downtime impacts regular operations and can have severe repercussions during peak seasons when heightened activity can escalate the risk and impact of equipment downtime. Similarly, in sectors where temperature-controlled shipments are vital, equipment failure can lead to losses in the form of spoiled goods. And let’s remember creating a safe and productive workplace for employees is only possible when your equipment is maintained to minimize the chances of an unexpected failure.
So, how do you arm yourself against this invisible enemy known as equipment downtime? The first step is to understand what causes it.
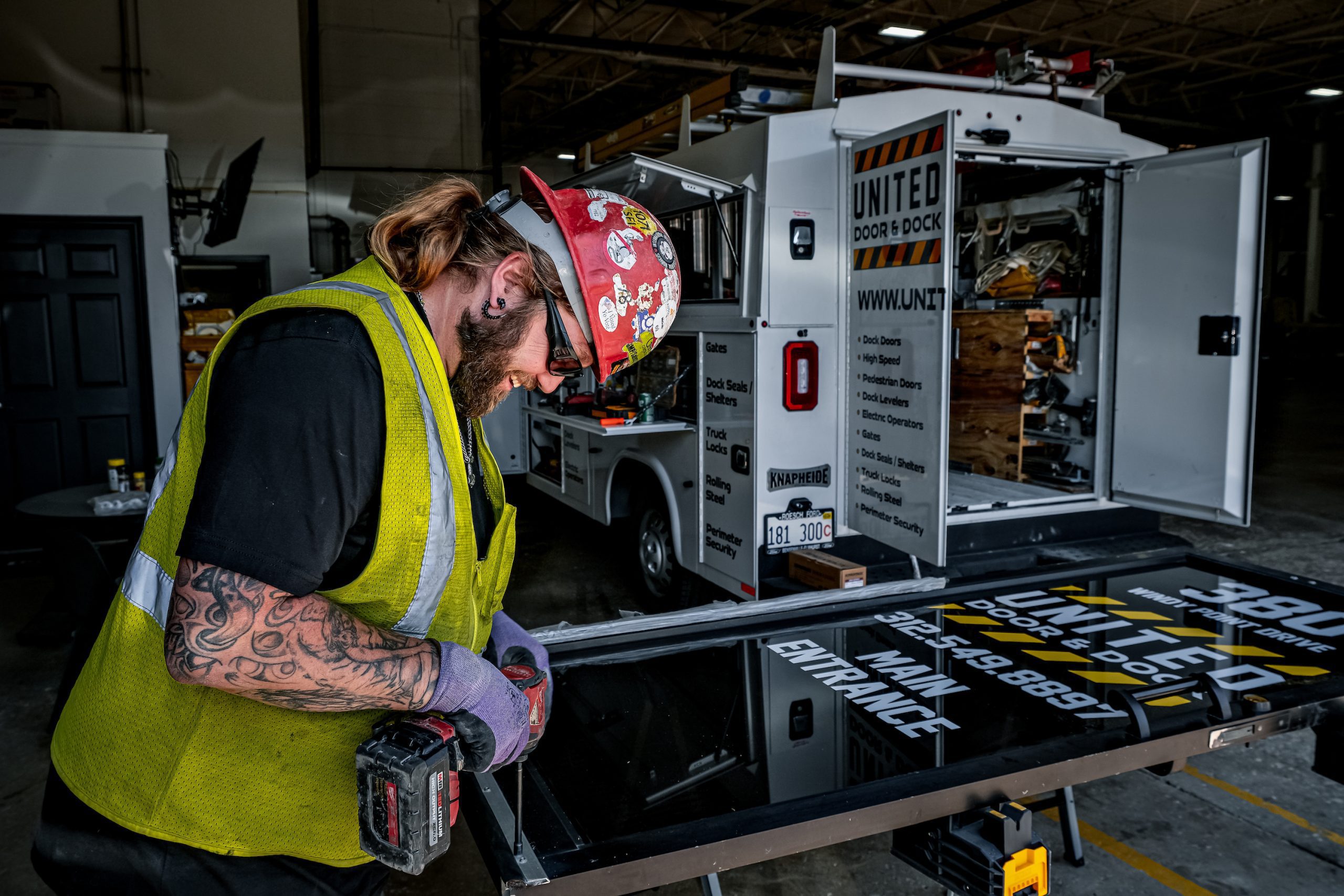
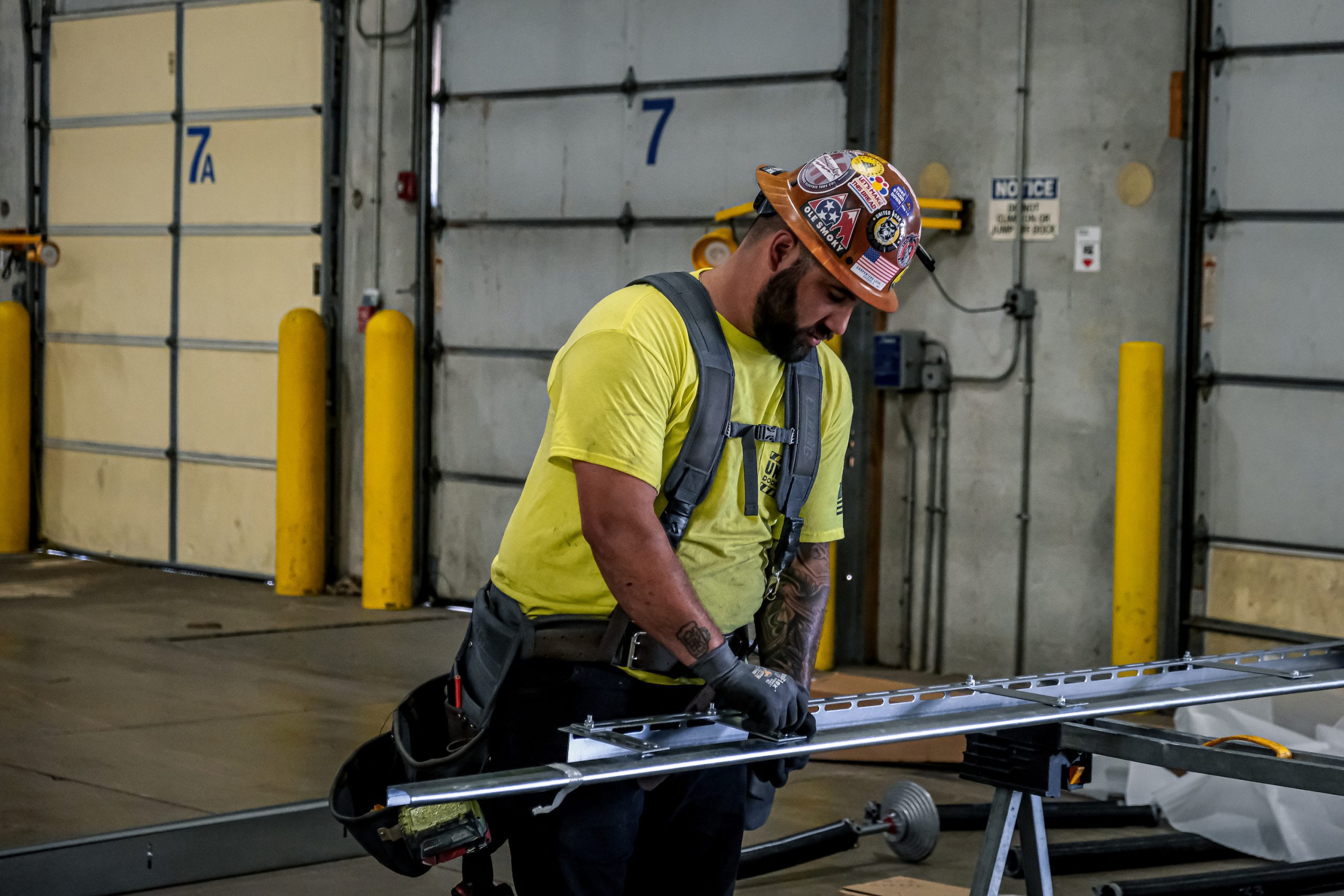
The Causes of Equipment Downtime
Some common culprits behind unplanned downtime in warehouses or distribution centers include:
The Cost
Unplanned downtime comes with both visible and invisible costs. These costs can have a significant impact on your bottom line. Let’s take a closer look at what you might face:
How to Reduce Downtime
Preventing downtime and increasing overall equipment effectiveness requires a multi-pronged approach. Here are some strategies you can adopt:
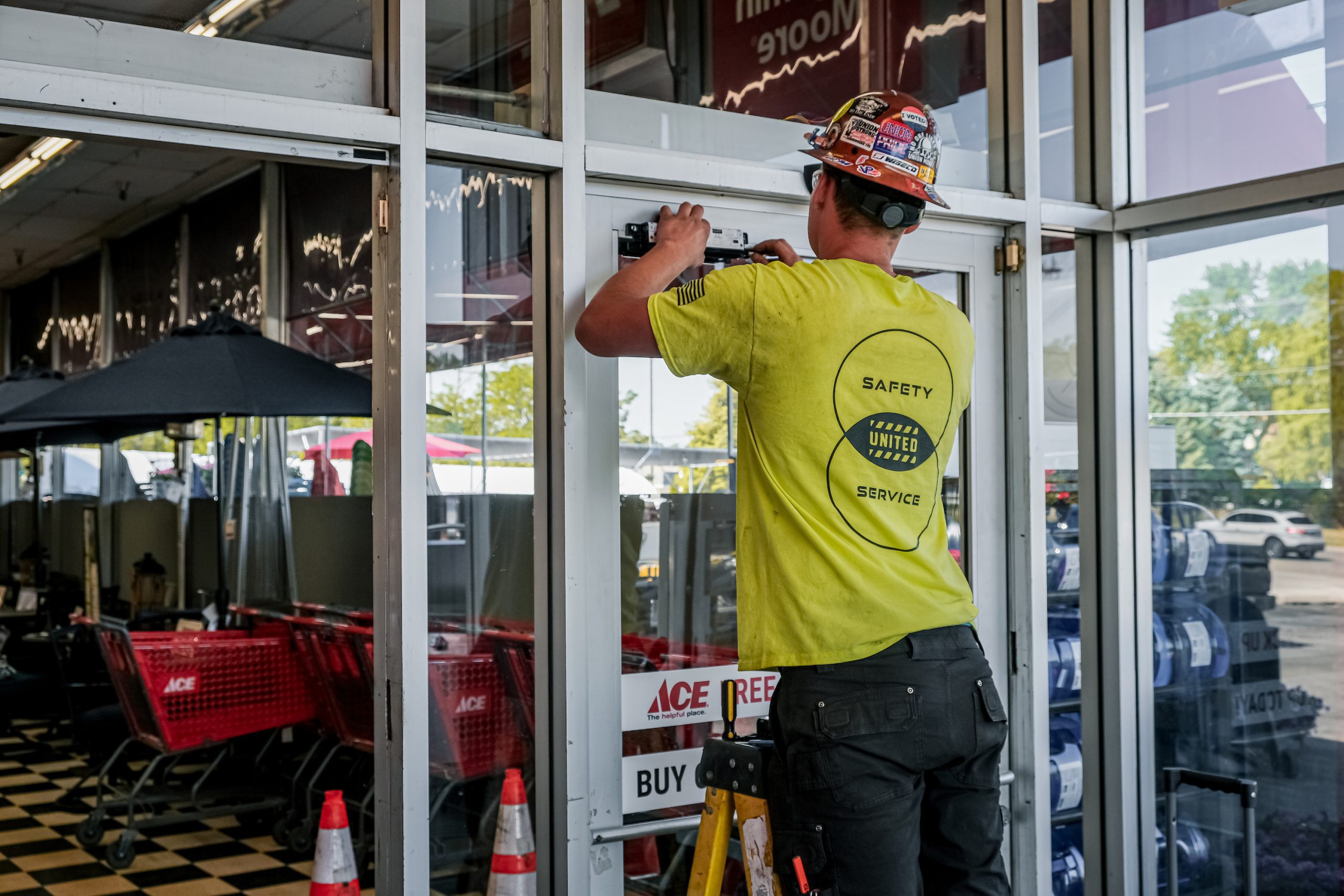
Adopting Proactive Maintenance with United Door and Dock
Partnering with an expert like United Door and Dock can drastically reduce your equipment downtime. Our professional team excels in providing proactive maintenance services designed to nip downtime in the bud before it wreaks havoc on your operations.
We believe in working hand-in-hand with you to understand your unique requirements and design a maintenance strategy tailored to your needs. Whether you’re running a single local warehouse or managing a nationwide chain of distribution centers, we can provide consistent, top-notch service that keeps your equipment humming and your operations flowing smoothly.
When you partner with United Door and Dock, you benefit from our proactive approach to equipment maintenance. We go beyond fixing issues and focus on selecting the right equipment for your specific needs and ensuring expert installation. Our team conducts regular inspections to identify potential problems early on so we can provide timely repairs and prevent breakdowns.
We understand the value of data in modern warehouse management. We can assist you in developing a detailed equipment inventory, tracking service life, performance, and potential issues. This visibility allows for more accurate forecasting, smarter budgeting, and more efficient operations. They can make informed decisions about maintenance schedules and allocate resources.
Remember, prevention is better than cure. By adopting proactive maintenance and working with experienced professionals like United Door and Dock, you can stay ahead of potential problems, extend the lifespan of your equipment, improve workplace safety, and, ultimately, reduce costly downtime.
Feel free to contact us and request a quote for planned maintenance, emergency repair service, and more. Let’s join forces to keep your equipment running smoothly, minimizing downtime and maximizing productivity.
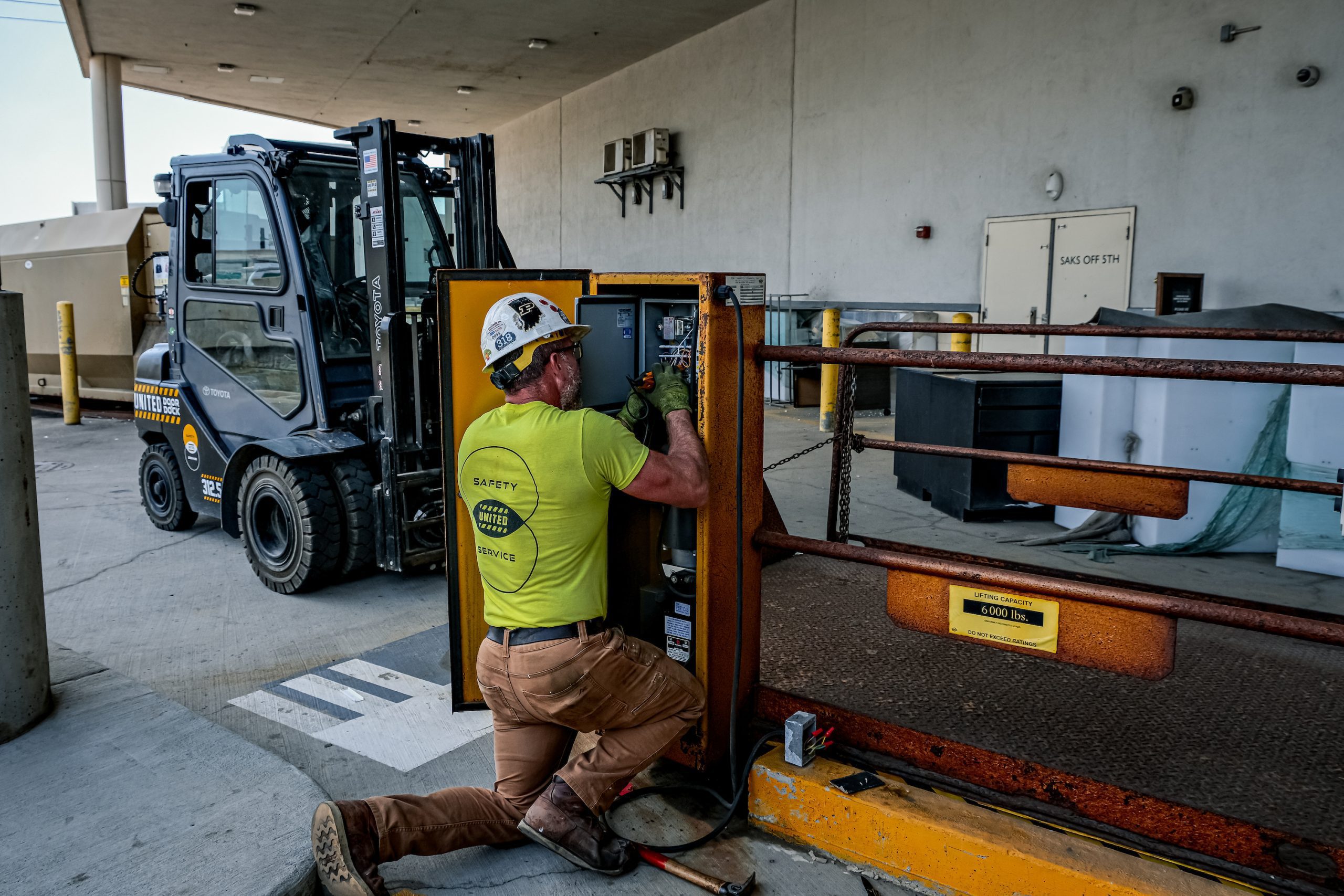
From Threat to Opportunity
By understanding the causes of equipment downtime and implementing proactive strategies, you can minimize the risk and impact of unexpected breakdowns. Careful equipment selection, equipment inventory management, and proactive maintenance are essential components of an effective approach.
Partnering with experts like United Door and Dock can further enhance your efforts in reducing downtime. As we said before, our proactive maintenance services, expert installation, and comprehensive training programs can keep your equipment in optimal condition and empower your team to identify and address potential issues.
Take the necessary steps to protect your business from the costly consequences of equipment downtime. Reach out to United Door and Dock today to strengthen your defenses and ensure the efficiency and profitability of your warehouse operations.